1. What is silicon steel
Silicon steel refers to Fe-Si soft magnetic alloy, also known as electrical steel. The mass percentage of silicon steel Si is 0.4%~6.5%, with high permeability, low iron loss value of excellent magnetism, with low core loss, high magnetic induction strength, good punching property, good surface quality of steel plate, good insulating film performance and so on. Silicon steel is mainly used for the preparation of various electric motors, generators and transformers and other power equipment core, is an indispensable metal functional material in the power, electronics and military industry, but also the key material for power equipment to improve efficiency and reduce energy consumption. As the largest amount of soft magnetic alloy, electrical steel is widely used in all aspects of the real economy, improving its overall performance and manufacturing level has a very important role and significance in the development of the national economy.
2. Development history of silicon steel
Before the advent of silicon steel, iron cores had been made of industrial pure iron. In 1886, Westinghouse Electric Company of the United States made transformer lamination core with a hot rolled low carbon steel plate with an impurity content of about 0.4%, but the low carbon steel has low resistivity, large core loss, high carbon and nitrogen content, and serious magnetic aging. In 1902, Gumlich found that the addition of silicon can increase the resistivity of iron, reduce eddy current loss and hysteresis loss, increase the permeability, and reduce the magnetic aging phenomenon.
1882~1995 is mainly the development stage of hot rolled silicon steel. In 1903, the United States and Germany first began to produce hot-rolled silicon steel. In 1905 the United States (the United Kingdom in 1906) has been mass production, in a very short time all replaced the ordinary low carbon steel plate manufacturing motor and transformer. Due to the magnetic induction, iron loss, punching and shearing workability, surface quality and insulating coating quality properties of cold-rolled non-oriented silicon steel are greatly superior to hot-rolled silicon steel, and hot-rolled products can not be rolled production, reducing the punching efficiency, the main industrial developed countries in the 1960s have stopped the production of hot-rolled silicon steel. In 1957, the former West German Ashims produced a double-oriented silicon steel sheet (cubic textured silicon steel) in the laboratory. It has high magnetic properties along the rolling direction and horizontally, but it is still in the laboratory stage and has not been put into industrial production.
From 1930 to 1967, it was mainly the development stage of cold-rolled ordinary oriented silicon steel (CGO) plate. In 1933, Gauss used two cold rolling and annealing methods to make 3%Si steel with magnetic high along the rolling direction. In 1935, the Armco Steel Company of the United States began the production of cold-rolled oriented silicon steel in cooperation with Westinghouse Company using Gauss patented technology. After 20 years of continuous development, Armco company in the mid-1950s to perfect a secondary cold rolling grain oriented silicon steel production process, that is, Armco process, since then, Armco process has long monopolized the world's cold-rolled oriented silicon steel production, ordinary oriented silicon steel (CGO) output of about 80% are produced in accordance with Armco patents.
From 1961 to 1994, it was mainly the development stage of high magnetic induction oriented silicon steel (Hi-B). In 1953, Satori Tanaka and others from Nippon Steel Co. in Japan proved that it is possible to make more magnetically oriented silicon steel with AIN as the main inhibitor and a single high reduction rate cold rolling process. In 1961, on the basis of the introduction of Armco patents, the first trial production of AlN+MnS comprehensive inhibitor of high magnetic induction oriented silicon steel. Production began in 1964 and was named Hi-B, but it was magnetically unstable. Since 1968, when Nippon Steel Corporation developed high-magnetic orientation silicon steel products, Japan's cold-rolled electrical steel has surpassed the United States in product quality, manufacturing technology and equipment, new technology development, experimental research and testing technology, and is in an absolute leading position in the world.
China's Taiyuan Iron and Steel works in 1952 the first trial production of hot rolled low silicon steel plate (1%~2%Si), 1954 formal production. In 1957, 3%Si cold-rolled oriented silicon steel was successfully developed by the General Institute of Iron and Steel Research. By 1973, China had mastered the main points of Armco technology patent, and Angang tried to produce it but failed to produce it. In 1974, Wuhan Iron and Steel Company introduced cold-rolled oriented silicon steel manufacturing equipment and patents from Nippon Steel of Japan. From 1976 to 1977, the General Institute of Iron and Steel Research developed Hi-B-oriented silicon steel on the basis of verification and digestion of Japanese patents. In 1979, WISCO officially produced oriented silicon steel, and so far, WISCO is still the main production base of oriented silicon steel in China.
3. Classification and use of silicon steel
3.1 Si quality score
Silicon steel according to the Si mass fraction classification is divided into Si<0.5% electrical steel and 0.5~4.5%Si silicon steel two categories, both known as electrical steel plate. The former in the manufacture of electromagnetic performance requirements are not high in the field of civilian small electrical appliances have a wide range of demand, such silicon steel sheet is characterized by the silicon content is significantly lower than conventional electrical steel, the preparation process is simple, low cost, and common carbon steel similar. The types and grades of the latter are extremely complex.
High silicon steel refers to 4.5%~6.7%Si Si-Fe alloy, which has the characteristics of significantly reduced iron loss at high frequency, high maximum permeability, low coercivity and extremely excellent magnetic properties, mainly used to manufacture high-frequency motors, high-frequency transformers, choke coils and high-frequency magnetic shielding. However, due to the high Si content, the plasticity is very poor at room temperature and can not be rolled. 6.5%Si has its own system because of its unique magnetic properties. At present, only a small amount of non-oriented 6.5%Si-Fe alloy materials prepared by siliconizing process can be supplied in rolls, and the preparation of more advantageous oriented 6.5%Si-Fe alloy is more difficult.
3.2 Production Process
According to the production method can be divided into hot rolled electrical steel and cold rolled electrical steel. Hot-rolled silicon steel sheet has been phased out in recent years due to its backward performance.
The most widely accepted method is to divide silicon steel into unoriented and oriented according to the degree of crystal orientation aggregation. Cold-rolled non-oriented silicon steel refers to 0.5% to 4.0%(Si+Al) alloy, cold rolled to 0.65mm, 0.5mm and 0.35mm after annealing coating made. Compared with oriented silicon steel, its grain texture type is more diffuse, has more uniform magnetic properties in all directions, and has low magnetic anisotropy, and is mainly used as the core lamination of various types of motors and generators. The thickness accuracy, dimensional tolerance grade and surface smoothness of cold-rolled products have reached a high level, thus improving the lamination coefficient and the magnetic properties of materials.
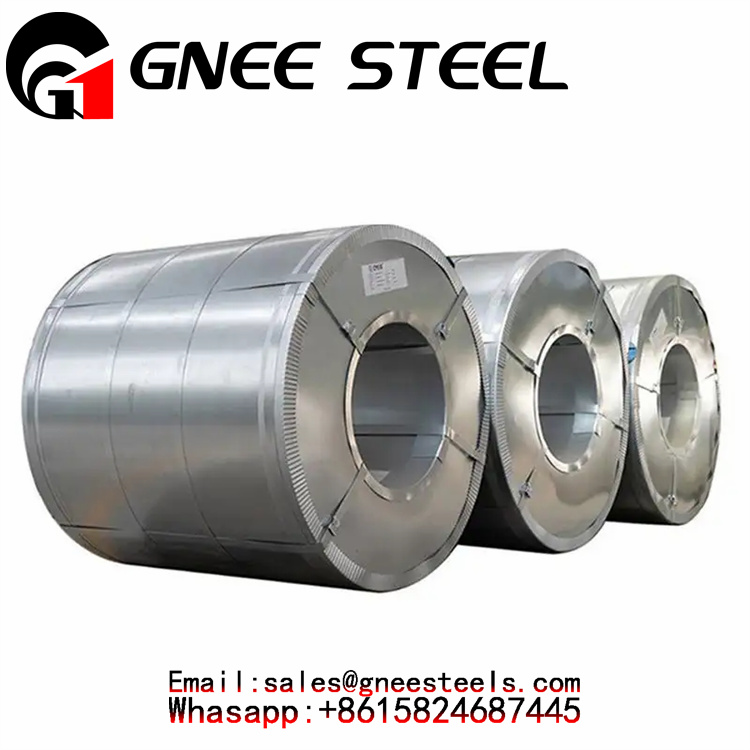
.jpg)